Glitter-Tailed Rocket with Willow Diadem Horsetail Finish
Introduction
What do I mean by a "spectacular" black powder rocket?
By this term, I am thinking of a great looking rocket, with a unique tail as it ascends, followed by a long-lasting, eye-catching heading. Maybe I have in mind a rocket that I wouldn't know how to improve on. (Of course, I am playing with two-pound versions of this baby already, since bigger is almost always better, or at least different.)
Here is a video of the rocket we are about to make, to get your juices flowing, and so that you don't have to read all the how-to information before you get to see what it is we're trying to accomplish.
Homemade Black Powder Rocket with Ascending Glitter Comet and Horsetail Header
You'll notice that the rocket does not fly into the stratosphere. It stays relatively low, allowing the audience to watch the graceful, arching glitter trail, and then to be close enough to the sparking horsetail header finish to be able to really appreciate it. This was all done by design, and I wanted this to be a really satisfying "fireworks rocket", not a high-powered machine.
I've described end-burning black powder rocket-and-girandola motors, but this project will focus on core-burning rockets.
In a past article John Werner discusses the construction of core-burning, black powder rockets, specifically 1/2-inch ID (4 ounce) models. John is a master pyro craftsman, and his articles are well-written, detailed, and complete. This one is no exception.
Toward the end of his article, after describing the rocket's construction in detail, John includes a "Troubleshooting" section, some options for "Modifications and Enhancements," and answers to some "Frequently Asked Questions."
I don't believe in constantly reinventing the wheel, so I'll simply use John's article as a foundation and base of reference for this one. I will be constructing 3/4-inch ID, one-pound, rockets in this project.
When I wrote my first article for Skylighter I focused on making clay nozzle and bulkhead mix, and I will be using those mixes in this project.
I've discussed black powder techniques and that BP will be used in the shell headers for these rockets.
I will be cutting and treating tubes, Skylighter #TU1065.
I've discussed making small plastic can shells and those small shells will be used as the headings on the rockets made for this article, with some minor modifications in technique.
I showed how to pump stars and make blackmatch in Tiger Willows in 2-1/2 Days, Day 1, and how to prime stars in Tiger Willows in 2-1/2 Days, Day 2, and I'll make stars and blackmatch using those techniques, with a special star formula for these rocket headings. (Flying fish fuse could also be used in this project with a nice effect.)
Quickmatch pipe was illustrated in Tiger Willow Shells in 2-1/2 Days, Day 3, and I'll be using some of that this time around, too.
And, last but not least, I'll be showing how to attach glitter comets, to achieve an extraordinary rising tail with these rockets.
Special techniques for finishing the rockets will be described so that the finished product will be safe and look nice even before it is fired.
So, you can see that all the skills and techniques that have been described in the newsletter articles of the past years start to build on themselves and come together in this stunningly beautiful rocket I'm about to describe.
You have your homework. Fire up your printer, and get the above mentioned articles in front of you. Study them, and assemble your materials. Then we'll get to work.
Note: One thing you'll hear from experienced fireworkers is, "Always take good notes about your experiments and projects, and keep them in a good notebook for future reference. A year from now you won't be able to clearly remember which of those experiments was the one that worked so well if you don't take good notes."
One of the extremely beneficial things about writing these Skylighter articles is that they then serve as my notes, when I might have been too lazy to follow the above advice otherwise. I also have access to the notes of others like John Werner. If you print out the articles, and then annotate them with your own modifications, they can serve as your notes as well.
The Plan
In Tiger Willow Shells in 2-1/2 Days, Day 1, 2, and 3, I described the process of making 8-inch tiger willow shells at a fireworks event such as a local club gathering or the annual PGI convention.I think I'll approach this rocket project in the same way, wherein a fireworker travels to a pyro event with absolutely no complete pyrotechnic materials, and makes everything from scratch at the event, and only in the quantities needed for this project. This eliminates any worry about licenses, storage, or transportation.
In Fireworks Tips #111, Harry included a shot of him and me at the most recent PGI convention out in Gillette, Wyoming. One of the great things about the convention is the opportunity to work alongside others as fireworks devices of all sorts are constructed.

An Empty Room Transformed into a Pyrotechnic Playground

16-Inch Ball Shells Were Made and Shot the Next Day

Members like Dan Thames Constructed Fancy, Two-Stage Rockets and Some Real Monsters

Tony Stader Building His 14-Foot Girandola

Kids Like Sarah Widmann Could Even Get in on the Act
Speaking of kids at the PGI convention, the Junior Pyros there always plan and execute one of the best shows of the week. The next generation of fireworkers is nurtured and brought along slowly and safely. Where would I be now if I'd started in all of this at the age of 15 instead of 35?
So, let's imagine we are bringing some materials and supplies to the PGI convention, and we are going to build a few of these fine rockets. I'll actually scale this project so that 10 of these babies can be constructed in a two-day period.
I will arrive on site, and begin building on Friday morning, with the goal of flying some rockets Saturday night. I'll want to plan my activities according to a time-line.
Before I even leave for the event, I accomplish a few things on the project:
- Print out all how-to articles and formulae.
- Unwind 40 feet of 16-ply cotton string with which to make black match.
Untwisted 16-Ply Cotton String
- Clean all my rocket tooling and lubricate with Sailkote (by Team McLube, available online or at sailboat distributors). This is a great lubrication product, which allows the tooling and spindle to release very easily from the rocket motor and tube. I also spray it on my star plates, comet pumps, and the aluminum rod I roll my match-pipe on.
SailKote Spray Lubricant
- Treat and cut my rocket tubes to 7-1/2 inches.
Ten 3/4-Inch ID, 7-1/2-Inch Long, Rocket Tubes
- Roll twelve, 18-inch lengths of paper quickmatch pipe
Paper Match Pipe for Quickmatch
-
Rip rocket sticks on my table saw. I like to rip sticks out of clear poplar from Home Depot. A 5-foot piece of 1x3 will yield 18 sticks, 5/16-inch square. It is also possible to use round wood dowels, but I much prefer square sticks. 5/16-inch square sticks are nice because I can rip a 5/16-inch wide by 3/4-inch strip off my 1x3, and when I rip that strip in half, my 1/8-inch thick sawblade leaves two 5/16 x 5/16 square sticks.
Bundle of Freshly Cut Rocket Sticks
- Making 40 feet of blackmatch
- Making 10.5 ounces of black powder for header-burst, and for star and comet priming
- Mixing, dampening, screening, and drying the rocket fuel
- Pumping and priming stars
- Pumping and priming glitter comets
Starting the rocket, Friday morning
I first set up my work station; I have a pop-up tent, work tables, and a chair. I'll need extension cords and a generator if no electricity is available where I'll be working. I might need a light if I get delayed too much on my timeline as I chat with pyro-pals. Some plastic sheeting can come in handy in the case of a sudden rain shower.I have my drying chamber in which to dry various products as they are produced. It'll be especially handy to have an electric outlet somewhere, even if it's not right at my work station, so that the dryer can be plugged in there and left running all night long.
I have my tool box with my miscellaneous hand tools, my measuring cups and spoons, my little digital scales, some funnels, my miter box and saw for cutting tubes on site, and the various supplies which will be mentioned as I go along.
I've brought along some food and a cooler of drinks, so I don't have to pause for long in the midst of my pyro activities.
Note: As I go along describing this project, I'll be applying materials and methods that I have described in the articles above. I will not be re-citing those articles in the text below. I'll trust you have the references available and are familiar with them.
Making blackmatch
I take the 40 feet of my untwisted string and make blackmatch out of it. It's a nice, warm, sunny and breezy day, so I string it up between two trees, tied onto nails, to dry. Before it gets dark, I'll cut it into 18-inch lengths and put it on a screen in the drying chamber.For this batch of match, I used a formula with a slight variation. 15 ounces of potassium nitrate, 3 ounces of commercial airfloat charcoal, 2 ounces of sulfur, 0.8 ounce of dextrin, and 0.2 ounce of CMC (Skylighter #CH8080). This batch took about 14 ounces of water, added carefully and stirred in with a paint stirring stick, avoiding getting the slurry too wet.
Replacing one-fifth of the dextrin in the original formula with the CMC produces a nice, smooth black powder slurry, which does not separate as I use it, and which produces a nice, smooth coating on the string.

Black Match Ready for the Drying Chamber
Making 10.5 ounces of black powder
I run 7.5 ounces of potassium nitrate, 1.5 ounces of airfloat charcoal, 1 ounce of sulfur, and 0.5 ounce of dextrin through my 100 mesh screen and onto a piece of kraft paper. I know from experience whether or not the individual chemicals will pass the 100 mesh screen, and if one won't, I'll run it through my blade-coffee-grinder first to pulverize it. I never run mixtures through the grinder, only individual chemicals.Then I run the mixture through the 40 mesh screen in order to intimately mix it.
I weigh 3 ounces of this mixture into a plastic tub, add enough water to it to make a putty out of it, and grate it through the 4 mesh screen. This will become black powder granules to be used to burst the shell headers. I have determined that it will take 0.3 ounce of this powder for each of the ten headers.
This granulated black powder, made with dextrin as the binder and not ball-milled, is called "polverone" rough powder (see Pyrotechnica IX, Traditional Cylinder Shell Construction, by A. Fulcanelli), rather than a hot black powder. I don't want a hot powder; I simply want to ignite the stars in the headers, and pop the headers open, allowing the lit stars to cascade down in a "horsetail" effect.
The remaining 7.5 ounces of the powder is set aside to be used for priming the stars and comets.

Granulated Polverone Black Powder
Making the rocket fuel
John Steinberg, Kurt Medlin, Steve Majdali, and Brent Anderson teach a "Black Powder Rockets for Beginners" seminar several times throughout the PGI convention week each year. It's a wonderful, hands-on seminar in which the basics of BP rockets are taught, and folks actually get to make a rocket of their own to take out to the rocket range and fly.They use a rocket fuel formula which creates a pretty rocket tail during flight, has enough power to lift a nice heading, yet is foolproof enough that even beginners can ram a rocket and have it fly every time.
Each of the ten motors in this project will use 2 to 2.5 ounces of the fuel, so I'll make up a 24-ounce batch of it.
That formula is:
Basic Black Powder Rocket Fuel | Ratio | 24-ounce batch |
Potassium nitrate | 0.6 | 14.4 ounces |
Airfloat charcoal | 0.1 | 2.4 ounces |
80-mesh charcoal | 0.18 | 4.3 ounces |
36-mesh charcoal | 0.02 | 0.5 ounces |
Sulfur | 0.10 | 2.4 ounces |
The potassium nitrate, airfloat charcoal, and sulfur are all screened through the 100 mesh screen. Then the coarse charcoals are added to the mix and it is all screened through the 40 mesh screen 3 times, and shaken in a closed tub to completely mix it.
Then enough water is sprayed onto the powder to dampen it to the consistency of brown sugar: just slightly damp, so it will barely stay together in a ball when squeezed in a fist. The water is worked in with gloved hands, and the fuel is pushed through the 16 mesh kitchen colander screen several times to fully integrate the moisture.
The fuel is then pushed through the 8 mesh kitchen colander screen and onto kraft-paper-lined screens to sit out in the sun and breeze during the day. I bring it in to dry in the drying chamber overnight.
The dry, mixed powder, can be used as-is before granulation, but wetting and granulating it significantly decreases dust during the motor ramming and probably increases the power of the fuel.

Rocket Fuel Drying on Kraft-Paper-Lined Tray
Making stars for the rocket headings
I want a slow-burning star which will form a "horsetail" when ejected from the rocket headings. One of my favorite stars is Willow Diadem, which is a long-burning, charcoal, Willow star, with the inclusion of some Ferro-Titanium and Titanium for metallic sparks in the stars' tails as they fall.I'm going to use 2 ounces of the stars in each of the 10 rockets, for a total of 20 ounces of stars.
Willow Diadem Stars | Ratio | 20 ounce batch |
Airfloat charcoal | 0.39 | 7.8 ounces |
Potassium nitrate | 0.31 | 6.25 ounces |
Sulfur | 0.11 | 2.15 ounces |
Dextrin | 0.07 | 1.4 ounces |
Ferro-titanium 30-60 mesh | 0.05 | 0.9 ounces |
Ferro-titanium 40-325 mesh | 0.05 | 0.9 ounces |
Titanium, medium spherical | 0.03 | 0.6 ounces |
Note: The original formula, as it has been passed around, specifies the metals as fine FeTi, medium FeTi, and medium Ti sponge.
This composition is made into 3/8-inch pumped stars and primed on one end. To prime them, I simply spritz them with a little water as they all stand on end in a tray, dust on a little of the BP prime that was set aside earlier, and spritz them lightly again. Then I tumble them a bit and place them on a drying screen.
Pressing the rising tail comets
The plastic can shells that I'll be using for the rocket headers are 2 inches in diameter, so I want to press 1/2-inch thick comets that same diameter. Each of these will use 1.5 ounces of D1 glitter composition, so I want to mix up 15 ounces of it.D1 Glitter | Ratio | 15-ounce batch |
Potassium nitrate | 0.53 | 7.95 ounces |
Sulfur | 0.18 | 2.7 ounces |
Airfloat charcoal | 0.11 | 1.65 ounces |
Aluminum, 325 mesh atomized | 0.07 | 1.05 ounces |
Sodium bicarbonate | 0.07 | 1.05 ounces |
Dextrin | 0.04 | 0.60 ounces |
This composition is mixed, dampened, and pressed into the comets, and then primed.

Stars and Comets Drying on a Screen
Saturday morning
Everything that was in the drying chamber overnight is dry as a bone this morning. It's time to start making some rockets.I'm going to assemble the headers first. These small shells will be identical to the 2-inch plastic can shells I described in Fireworks Tips #112, with a couple of exceptions.
Note: Similar headers can be assembled using kraft paper, paper discs, chipboard or manila folders, and glue if plastic shells are prohibited at a particular shoot site.
The fusing on the bottom of the shell will be quickmatch instead of time-fuse. I want the headers to pop at the same moment the rocket fuel burns out and passes fire out the top of the motor and to the header.
I cut a 1/2-inch long piece of the paper match pipe, insert two 2-inch pieces of the blackmatch (cut with anvil cutters or a razor blade), pinch the pipe around the match and fold over the excess paper pipe. This fuse gets glued (hot-glue on the outside only), into the hole I previously drilled in the bottom of the plastic can (not the hole in the shell cap).

Quickmatch Fuse Hot-Glued into Hole in Plastic Can Shell Casing
Then 0.3 ounces of black powder is poured into the shell, the tissue paper disc inserted, and then the stars are added.
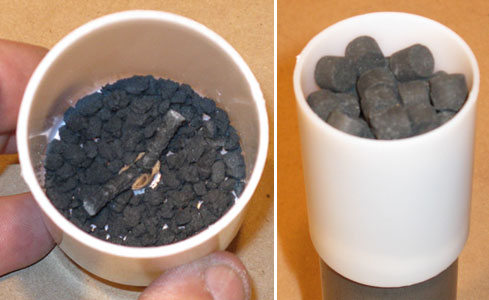
Black Powder, Tissue Paper, and Stars Placed in Shell Casing
I use a coping saw to remove the fuse-hole protrusion from the plastic casing cap, and then I use PVC plumbing cement or thickened methylene chloride to glue the cap on the shell. The capped shell can be tapped with the handle of my awl, and as many more stars as possible can be introduced through the hole in the cap.

Cutting and Gluing on Plastic Shell Casing Cap
Next, a 1-1/2-inch paper disk is hot-glued into the recess of the shell's cap; then a 2-inch disk is glued on; and finally the comet is glued on.

Two Paper Discs and Comet Hot-Glued onto Plastic Can Shell
And that completes the assembly of a rocket header.

Completed Comet and Shell for Rocket Header
Ramming rocket motors
My work table has been cleaned up from the previous processes, and I've laid out my materials for ramming the rocket motors. Nozzle clay mixture, bulkhead clay mix, rocket tubes, rocket tooling, pounding post, rawhide mallet, 1/2-tablespoon measuring spoon, funnel, rocket fuel and paper cup.
Tooling and Materials Assembled and Ready-to-Ram Rocket Motor
The pounding post I actually use is 24-inches long. I like to work with a small amount of rocket fuel in a paper cup, keeping the tub of fuel closed rather than having it sitting open with all that fuel exposed.
All my tooling drifts have rubber o-rings on them to further minimize dust, which has already been reduced by granulating the fuel. The drifts also have 'do-not-pass' marks on them so they don't hit or get stuck on the spindle.
When hand-ramming these motors with the specified tubes, a tube support-sleeve is not necessary. Care must be used with the ramming/hammering so that I achieve good, consistent consolidation, without over-stressing or splitting the tube.
Note: I suppose the first real question that popped into my head back when I first assembled the materials to ram rockets was, "How will that dry clay and rocket fuel stick together with just pounding on it? Don't I need to moisten it or something?"
The answer is, "Nope." The dry powders will consolidate into a solid grain simply with the pressure of the ramming process. Pretty amazing!
Below is the kind of drawing I sketch up for each of my types of rockets once I dial them in. The sketches enable me to come very close to duplicating my results each time I make up another rocket of that type.
Of course, the details of the sketch will vary according to the exact tooling, tubes, and materials that are being used. But, if I keep those the same from batch-to-batch, the sketch becomes very useful.

Blueprint for One-Pound Black-Powder Rocket Motor
A tube is placed on the spindle, a flat 1/2-tablespoonful (0.35 ounce) of the nozzle mix is placed in the tube, along with the nozzle forming drift. Then, 8-10 solid whacks with the rawhide mallet will form the nozzle. I try to ram the tube hard enough to create a very small bulge in the area of the nozzle, without it being seriously deformed or split. This seats the nozzle more securely and reduces the chances of it being blown out.
I have determined that this amount of pounding is equal to 1000 pounds of force being applied to the hollow drift, which is equal to about 3000 psi of pressure being applied to the composition. These are the figures I would use if I was using a hydraulic press to press these motors. With 1000 pounds of force, and with the solid drift, about 2300 psi would be applied to the composition.
When I begin to ram the fuel grain in the motor, I weigh out the amount of fuel that will be rammed with each drift, according to the specifications I've noted on the sketch, and put it in the paper cup. Then I scoop the fuel out of the cup, one increment (1/2 tablespoonful) at a time, until that amount of fuel has been rammed. Then I know it's time to switch to the next drift, and I weigh out the total amount of fuel to be rammed with that drift.
This keeps me from having to constantly be counting the number of increments I have rammed, or guessing if it's time to switch to the next drift.
The delay fuel at the top of the motor, approximately 0.3 ounce of it, is weighed out, and I add a flat 1/8 teaspoonful of fine spherical titanium to that fuel and swirl it around in the paper cup to mix the metal in. Then I ram those increments of delay fuel into the motor, being careful to only bring the fuel grain up to between 1 and 1-1/16 inches above the spindle.
This amount of delay fuel gives me the proper delay between the powerful thrust fuel burn, and the heading burst. When I was dialing the motors in, it is this amount of delay fuel that I adjusted to get the heading to burst at just the desired point in the rocket's flight.
Once the delay fuel has been rammed up to the correct height, I plunge the open end of the motor into the bulkhead clay to pack the void full of that clay. Then I scrape off the excess clay, and ram the bulkhead.
Using a 1/4-inch drill bit, I carefully hand-twist-drill a hole in the bulkhead, just barely into the fuel grain. This creates the passfire hole which will transfer fire from the motor to the heading when all the motor's fuel has been spent.
Twisting the motor off the spindle reveals a nicely formed central cavity. The motor is now ready for the final rocket assembly.

Bulkhead and Nozzle Ends of Black-Powder Rocket Motors
Final Rocket Assembly
Whew! The hard part of this project is done. Now for the easy part.I trim the black-match sticking out of one of the headers so that it is just long enough to go all the way to the bottom of a motor passfire hole when the header is pressed onto the motor. Then I hot-glue the header to the motor, and reinforce the assembly with some strapping tape.
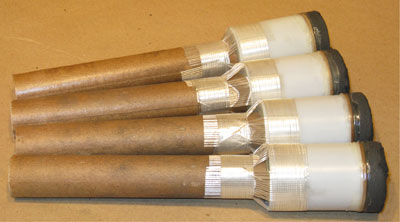
Rocket Motors with Headers Attached
Now I hot-glue and tape a 5-foot rocket stick to each motor. I glue the sticks on so that any bow in the stick curves it under the center of the motor. Instead of the stick curving out and away from the motor, or to the left or the right, I want it curving back in toward the centerline of the motor. I bevel the end of the stick with my anvil cutters to minimize drag (as if that big, clunky, flat-ended comet is aerodynamic).

Black Powder Rockets with Sticks Attached
It is now time to fuse these babies. I take two pieces of the black-match I made, and slide them into one of the paper match pipes. One of the pieces of match protrudes from the pipe 2 inches, and the other one only 1 inch. The pipe is crimped around the match for about 4 inches, and that end of the quickmatch is inserted into the rocket motor as far as it will go.
Then I bend the quickmatch leader up alongside the motor, and secure it to the motor and header with masking tape.

Quickmatch Fuse Leader Inserted into Rocket Motor and Attached to Motor and Header
The quickmatch is folded over to the center of the comet, and bent upward. Using the awl, a hole is pierced in the match pipe, and an additional 4-inch length of black-match is inserted into the pipe and bent onto the top of the comet. This end of the match will pass fire to the comet while the other end ignites the motor.
I want the comet to ignite just slightly before the rocket motor does, so that the comet is really emitting its fire as the rocket starts to ascend.
The quickmatch and black-match are held in place with lengths of masking tape, and the quickmatch is cut with the anvil cutters to a length of 3 inches above the comet.

Quickmatch Leader and Black-Match Passfire Attached to Top of Comet
An 8-inch square of light tissue paper or wrapping paper is wrapped around the comet and header, and hot-glued to itself only. This creates a loose wrap which will protect the comet from unwanted fire, but will burn and fall away as the rocket ignites and ascends. This wrapper is tied around the quickmatch leader.
A piece of visco fuse is secured into the end of the leader, and a reusable safety cap, made of more match pipe, is installed to protect all the fusing from sparks (and to make the whole deal look a little more finished and pretty.)
It's funny, but over the years I've seen other pyros who get to the point where they want to put as much effort into making the outside of their devices as attractive as they hope the performance of the inside will be.

Loose Protective Wrapping Installed Over Comet. Visco Fuse and Safety Cap Installed
The Finished Rocket
Two days. I started with nothing but a few chemicals, some materials, and a few basic tools. Now I have a finished product that I can watch the video of, and look at the photos of, and I can step back and say, "Yep, I'm proud of that." That's why I got into all of this in the first place.
Finished Black-Powder Rockets in the Air
I'm gonna go back and watch that rocket video a few more times.
I hope you can follow these tips, create some of your own tricks, and come up with something you can be really proud of. Perhaps we'll see the results at the next PGI convention.
'Til then, Stay Green,
Ned