Weighing and Screening Chemicals for Fireworks
Weighing out specific amounts of chemicals, and screening them together to form a composition, are the most basic firework making procedures. But, as with any skill required when making your own fireworks, these fundamental jobs can be done well or poorly, which will affect the final results of our efforts.
Indeed, weighing and screening are often the most time-consuming parts of making homemade fireworks. So, the faster and more efficiently you can learn to do these tasks, the more quickly you will be able to make fireworks.
Let's say that I want to make the Silver Titanium Fountain Fuel that was one of the compositions I made gerbs with in "Making Gerbs (Fountains)". This is one of my favorite fountain formulations and it is a simple one to start off with.
Silver Titanium Gerb/Fountain Fuel
Component | Percent | 16-Ounce Batch | 450-Gram Batch |
Potassium Nitrate | 0.51 | 8.15 ounces | 229.5 grams |
Sulfur | 0.10 | 1.6 ounces | 45 grams |
Airfloat Charcoal | 0.09 | 1.45 ounces | 40.5 grams |
Spherical Titanium | 0.30 | 4.8 ounces | 135 grams |
The original formula gives me the percentages of each firework chemical. Then I pick a batch size that is suited for the project I'm working on. In this case, I want to make five of the 3/4-inch ID fireworks fountains I described in that gerb article. Each fountain will use about 3 ounces of the fuel, or about 85 grams (approximately 28.4 grams in an ounce).
So, I settled on the 16-ounce/450-gram batch size. I multiplied the percentage of each component times the total batch size to determine how much of each chemical to use. For example, 0.51, the potassium nitrate percentage, times 16 ounces, equals 8.16 ounces. I always round these ounce amounts off to the nearest 0.05-ounce, so the 8.16 ounces becomes 8.15 ounces.
Similarly, if I'm going to be working in grams, 0.51 times 450 grams equals 229.5 grams. I round gram measurements to the nearest 0.5 grams, so this result does not have to be rounded.
Once I have calculated the individual amounts of each fireworks chemical in that size batch, I add them up to make sure they do indeed total up to the desired batch size, and to verify that I didn't make some mathematical error in my calculations.
Now I have the weights of each individual chemical I'll be using in the project. I print that page out to have it before me as I'm performing the next steps.
Digital Electronic Scales
I have two electronic digital scales I use only for weighing chemicals used in fireworks, one for large batches of more than a few ounces, and one for small batches of only a few ounces. I got these from my favorite fireworks-supply house.
The TL5030 scale will weigh up to 15-pounds/7000-grams with a precision of 0.05-ounce/1-gram. The TL5021 pocket scale will weigh up to 222-grams/7.8-ounces with a precision of 0.1gram/0.01 ounce. Both scales can be switched back and forth between ounces and grams.
Some pyros use mechanical, triple-beam scales to weigh firework chemicals. I've never done that, having started out with electronic, digital scales, and stuck with them ever since. Digital scales are faster to use; they give you an instant readout. You don't have to twiddle your thumbs waiting for that annoying beam to finally stop swinging up and down.
But, the electronic scales can go bad now and then. It is hard to tell when they have done so, since quite often they simply start to become inaccurate as they weigh stuff.
For this reason, I keep five quarters (US 25-cent pieces), which weigh exactly 1-ounce/28.5-grams, in a little plastic baggie in my shop. Before I weigh out the chemicals in a fireworks composition, I weigh my test-quarters to make sure the scale is still functioning accurately.

Weighing out individual chemicals for fireworks
First, I get out the tubs of the 4 individual chemicals I'll be using, and place those containers on my workbench.I leave the titanium off to the side for now, because I do not put metals through my screens while I'm screening and mixing compositions. Fine metal particles can get lodged in the screen openings and be very difficult to remove, permanently clogging the screen, and possibly contaminating other compositions in the future. I'll add the metal to the composition later.
I store my fireworks-making supplies in their original containers, inside the inner plastic baggies, with the bags twist-tied closed, and the lids on securely. This helps prevent the chemicals from absorbing moisture from the air over time.
I also keep a dedicated, disposable, paper cup in each firework-supplies container, with which to scoop out that chemical. This is a very good way to prevent cross-contamination of one's chemicals. I like to keep my chemicals as pure as possible.
If I were to ladle out sulfur with a scoop, put that sulfur in my weighing container, and then remove some potassium nitrate with the same scoop, I have introduced sulfur into my potassium nitrate. The next time I use the nitrate, I may be using it in a composition in which I do not want sulfur; but there will be some residual sulfur in the tub regardless of my best intentions. That's not good.

If the chemicals are being weighed out for a batch, which will be going into the ball mill, where they will be pulverized, I don't worry about the individual powders being finely screened prior to weighing them.
But, in cases such as this fountain formula, where I'll simply be mixing the components together, and I want the individual chemicals to be finely pulverized, I screen those individual chemicals through a 100-mesh screen before weighing them. If they will not pass that screen, I pulverize them individually with the coffee-mill.
Once all the individual chemicals will pass the 100-mesh screen, it's time to weigh them for my fountain-fuel batch. My large digital scale came with a nice bin to weigh powders into. I place that on the scale, and tare the scale so that the weight of the bin is not included in the displayed weight. Taring the scale simply requires placing the bin on the scale and pushing the "tare" button, which resets the scale's readout to zero. This way, only the chemical placed in the bin is weighed on the readout.
Next to the scale, I place the plastic tub into which I'll be pouring the ingredients, after I weigh them. I could weigh one chemical at a time into the main scale-bin; and just tare the scale between chemicals.
But sooner or later (probably sooner) this will cause a problem: Too often, more chemical than I really want will pour out of my chemical scoop. If I am adding that chemical onto a previously weighed one, then I have to try to remove the excess second chemical without picking up any of the first one. This becomes a royal pain-in-the-butt and slows the process.
So, one chemical at a time is weighed out, then poured from the scale's bin into the mixing tub. As I said, I'm saving the titanium for the last step, so I don't weigh it now.

As a final double-check, I pour all the ingredients back into the weighing bin after they have been weighed individually and placed in the mixing tub. I see if the total weight is what I intended it to be: in this case, 11.2 ounces of the potassium-nitrate/charcoal/sulfur mixture.
This final quality-control check ensures that I have not forgotten any chemical, which is easy to do in formulas containing many ingredients. It also verifies I weighed each individual chemical correctly. This step can save many problems down the line.
Screen-mixing the chemicals
I know my chemicals all passed the 100-mesh screen individually, so after they have been weighed, I use the 40-mesh screen for mixing them together. All of the screening and mixing is done outdoors because highly flammable dust will be created that I do not want to accumulate on my workshop surfaces.Even working outdoors, I also wear a good dust-proof respirator and rubber gloves. Cotton clothing and eye protection are also musts. Long sleeve cotton shirts, and long cotton pants save lives every year. In a flash fire resulting from accidental ignition of mixed fireworks chemicals, the cotton may singe, but will not catch fire. Synthetics, on the other hand, will melt onto the skin in a fire.
I tear two pieces of kraft paper, slightly larger than my screen, off of my roll and place them, one on top of the other, under my screen. There are various on-line sources, such as www.uline.com or www.papermart.com for kraft paper and pull-and-tear dispensers for paper rolls.

The batch is gently poured from the mixing tub onto the center of the screen. Then I gently rub the composition through the screen, back and forth with my gloved hands, until all of it has passed through the screen.
The screen is picked up and set aside for a moment. The edges of the top sheet of paper are raised slightly to "roll" the composition towards its center, and that paper is picked up, too. The screen is placed on the remaining sheet of paper, and the composition is poured back onto the screen from the paper, which contains it.
The comp is rubbed through the screen a second time; the screen is set aside; and the sheet of paper containing the composition is picked up. The empty sheet of paper is placed on the workbench, and the screen is placed on it. The composition is screened for the third and final time, after which it is poured back into the mixing tub.
Screening the powder three times like this breaks up any clumps of the individual chemicals and intimately mixes them together into a homogeneous mixture.
I simply bundle up the sheets of paper, which were used for the screening and dispose of them in my burn pile.
The spherical titanium is now weighed out on the scale, and that metal is added to the mixing tub. The lid is securely installed on the bucket and the metal is incorporated into the composition by gently shaking the tub.
The composition is now ready for the next steps in the manufacture of the fountains.
Uses for screens in fireworks making
The framed screens we use in making fireworks can serve different purposes. These screens are typically specified in mesh-sizes. The mesh size refers to the number of wires there are in the screen, running one direction, per inch. So a 100-mesh screen has 100 wires running one direction per inch, and 100 wires running the other way per inch. That's some mighty fine wire.I just described above how the 100-mesh screen is used to make sure chemicals are pulverized down to at least a particular small size before mixing them.
The screens are then used in the intimate mixing of the chemicals into a formulation as I did with the 40-mesh screen.
Screens can also be used to size particles so that only that size is used in a composition. Charcoal can be specified in a range of mesh sizes, for example: 20 mesh, 36 mesh, 80 mesh, and airfloat. These different particle sizes serve different purposes in a charcoal composition.
Now, if I buy these charcoals from a firework-supply outlet such as Skylighter, I don't have to worry about separating the different mesh sizes. I'll get tubs of each individual mesh size, already sorted. But if I make and crush my own charcoal instead of some place that sells firework-making supplies, I'll have to have a way to separate, say, 80 mesh charcoal from 36 mesh charcoal from airfloat charcoal, if I want to use those particular mesh sizes, say, in a one-pound black-powder rocket fuel.
This is done by crushing my homemade charcoal and screening those crushed bits through various size screens to separate the specific sizes of particles.
If I have screens in various sizes, 10-mesh, 20-mesh, 40-mesh, 60-mesh, and 100-mesh, I can use them to sort out the various size charcoal particles.
I'll place my crushed charcoal on the 10 mesh screen and rub it on the screen. What falls through the screen is finer than 10 mesh, and what sits on the screen is coarser and will be set aside for more crushing.
I'll then put the charcoal, that passed the 10-mesh, on the 20-mesh screen and rub it with gloved hands. What won't pass the 20-mesh is sized between 10 and 20 mesh and is set aside.
What passes the 20-mesh is placed on the 40-mesh and rubbed again. What sits on the 40-mesh is sized between 20 and 40-mesh and is set aside. I keep doing this right down through my screens until what passes the 100-mesh screen would be considered airfloat charcoal, and might be ball-milled to ensure that it is as fine as possible.
So, I've ended up with charcoal in assorted particle sizes:
- Larger than 10 mesh to be crushed more
- 10-20 mesh
- 20-40 mesh
- 40-60 mesh
- 60-100 mesh
- Airfloat charcoal
I have the airfloat charcoal specified in the formula. For the specified 80-mesh charcoal, I can use the charcoal I sized to be between 60-100 mesh. And, for anything that calls for 36-mesh charcoal, the 20-40 mesh charcoal ought to work just fine.
So, screens in various mesh sizes can be used to sort out different chemical particle sizes. They can also be used to sort rolled-star sizes if I have screens in larger mesh sizes.
Often, for sorting star sizes, 8-mesh, 4-mesh, 3-mesh, and 2 mesh (sometimes called 1/2-inch mesh screen) are used. The wire takes up just a little bit of the space per inch of screen, but in rough terms these screens could be used to separate rolled stars into these different sizes:
- Larger than 1/2-inch
- 5/16-inch to 1/2-inch
- 1/4-inch to 5/16-inch
- 1/8-inch to 1/4-inch
- Smaller than 1/8-inch
How to frame your fireworks-making screens
Skylighter occasionally stocks pre-framed, round screens which are imported.They also sell un-framed, square sections of stainless-steel screen, 11.75-inches square, in the 10, 20, 40, 60, and 100-mesh sizes.
Larger mesh sizes are available from various online sources. These stainless steel screens are not inexpensive, but being stainless steel, they can last a long time, especially if they are secured into a well-built wood frame.
Here's how I would frame a 20-mesh, 11.75-inch square screen.
I want to end up with a wood frame, which is 1/2-inch smaller than the unframed screen in both directions. Having the screen overlap the sides of the frame helps when it comes to stretching the screen tight.
I like to make the wood frame 3.5-inches deep so that plenty of chemical can drop through the screen and accumulate on the paper as I'm using the screen, without piling up and clogging the mesh.
For that reason, I use 1x4 lumber, which actually measures 3/4-inch by 3.5-inches.
I prefer poplar wood, which is readily available from stores like Home Depot. Poplar doesn't have much grain, so it doesn't warp much. Although it is classified as a hardwood, it is soft enough for my nails and staples to be easily driven into the wood. Certainly other woods like fir, pine, oak or maple could be used, but I'd be afraid that my staples wouldn't drive well into the harder woods like the oak or maple.
I showed how I cut paper tubes with a hand miter box and saw in Fireworks Tips #107. If you don't have a power saw, this same setup can be used to cut the lumber in this project.
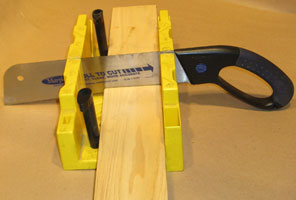
I cut four pieces of the 1x4, 10.5-inches long. This will result in a frame with 11.25-inch outside dimensions, which is 1/2-inch smaller than my screen.
At the same time I cut four, 11.25-inch-long pieces of 3/4-inch wide, pine half-round trim, also from Home Depot. These wood strips will form the trim, which will cover the edges of the screen once it is installed on the 1x4 frame.

I use some sandpaper to smooth the corners, edges, and ends of my wood. Then I apply two coats of fast-drying, spray polyurethane to all the surfaces of the wood before assembly. This finish will prevent the wood from soaking up water or chemicals over the years of use and cleaning that the screen will get.

After the polyurethane coats are dry, the 1x4 frame is glued and nailed together. I like to use 6d (2-inch) galvanized finish nails, and polyurethane construction adhesive when assembling the frame.
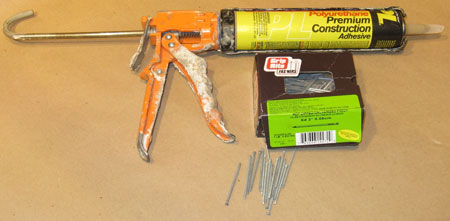
I pre-drill the nail holes with a 1/16-inch drill bit to prevent the wood from splitting when the nails are driven in. Then I put a thin line of the glue onto the joint, after which I install 3 nails in the joint.

Once the frame has been glued and nailed, I make sure it will sit flat on my workbench. I also check the two, diagonal, corner-to-corner measurements to make sure they are the same, which proves the frame is square. I make any adjustments necessary to ensure the frame is flat and square.
Time to install the screen: I use 1/4-inch long, galvanized staples, and a staple gun to attach the screen to the frame.
I first staple one of the sides onto the frame, with the screen in about 1/16-inch from the edge of the wood on two of the sides. I don't want any wire sticking out from the sides of the framed screen once it's done. Such wires could stick and cut my hands while I'm using the screen.
While I'm stapling this first side of the screen, I'm pulling it taut to make sure the side is stretched and straight as it is attached to the frame.

Then, as I make sure the screen is lying flat and that the second side is pulled square, tight and straight, I staple that second side to the frame. After each side is stapled, I hammer all the staples flush into the wood.

Now, I stretch the fourth, unsecured corner, out in the diagonal direction. This can be facilitated by inserting a sharp awl through the screen, and down into the wood. Then the awl can be "cranked" outward, stretching the screen in the process. This works best in the coarser-mesh screens. One has to be careful not to tear the screen when doing this with fine-mesh screens.

I staple the fourth screen corner while stretching it out tightly, and then I staple the third and fourth sides. As I staple those sides, I pull the screen outwards, holding onto the extra 1/2 inch of screen, and pushing the wood inward with my finger as I do so.
This slight inward bow of the wood will hold the screen tight once it's stapled. Having that 1/2 inch of screen to pull on, is why I made the wood frame 1/2 inch smaller than the screen in both directions in the first place.

Now, I can slice off the extra screen, in 1/16 inch from the outside edge of the wood, with a sharp razor knife. The knife can be used to cut screens up through 20-mesh. For coarser screens and wire, the screen must be cut to the final size initially, and the awl method must be used to stretch the screen throughout the process.
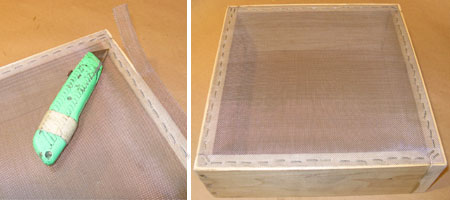
Warning: Please be careful when trimming with the razor knife. I've worked with power tools my whole life, and I've never injured myself worse than I have with one of these knives. They can slip during the cutting and stitches will be necessary. Keep your "other" hand out of the way as you use the knife. All of this is supposed to be fun. Let's keep it that way.
And, in a final step, I use more of the glue and some 1-inch, zinc-plated wire brads to install the 3/4-inch, half-round, trim strips. I like using this trim because the inner sloping edge directs the chemicals toward the screen, and the rounded profile is soft on the hands during use.

As I'm using the glue I'm careful to apply enough so that the screen ends up embedded in the glue, which is stuck to both the top and bottom wood surfaces. This ensures that even with pressure from the hands during use over the years, the screen will stay in place, good and taught and straight, instead of developing a downward bow.
But, I don't apply so much glue that excess oozes out as the trim is applied. That would make a mess and clog some of the pores in the screen. Any excess glue that is present once the wood trim has been installed is carefully wiped off with fingertips. Paint thinner will remove glue from the screen if this is necessary.
I make sure there are no wires or screen-edges sticking out before the glue is dry. If there are, I can trim them now and seal those edges with a bit more glue.
Conclusion
Well, there you have it; one of the basic tools of the firework making trade, hand-made, and fit for years of service. It will be a pleasure to use the screen each time it is picked up, knowing that it was well made with quality materials.When I'm done using the screen during a particular operation, I take the hose and thoroughly clean and dry it, storing it in a clean, dry location for future use.Enjoy and Stay Green,
Ned